Drilling Tools
The HDD Bottom Hole Assembly (BHA)
In drilling HDD projects, the away portion of the downhole drillstring just above the bit is called the bottom hole assembly (BHA). The BHA is different depending on whether a mud motor assembly is used, or a jetting assembly is used as shown in the diagram below.
The selection of a jetting assembly or a mud motor assembly strictly depends on the formations encountered by the drilling process. Softer formations, including unconsolidated sediments, and gravels may be drilled with a jetting assembly and hard rock formations are drilled with a rock bit and mud motor assembly. Mixed formations consisting of interleaved soft and hard formations should generally use a rock bit and mud motor assembly. The Bottom Hole Assembly used during a HDD project will impact not just on how quickly or efficiently a crossing is completed, but also on how easily the assembly can be steered to follow the designed profile.
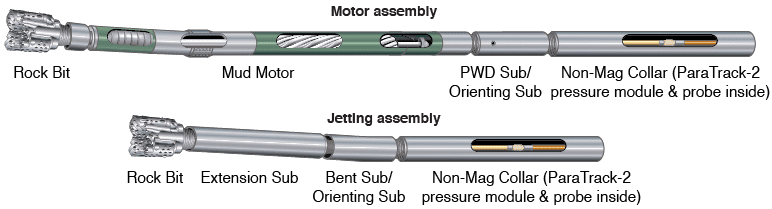
Mud Motor Assembly
The bottom hole assembly provides force for the bit to break the rock (weight on bit, or WOB), survive a hostile mechanical environment and provides the driller with directional control of the drillstring. The assembly will include a drilling bit, a mud motor with an adjustable bent sub for steering, a steering tool (ParaTrack-2), and other specialized devices like the Pressure While Drilling sub attached below the ParaTrack-2 Steering Tool to measure the annular pressure profile throughout the well bore. In the case of drilling intersect projects with two drilling rigs, one at the entry location and the other at the exit location, one drill string will contain the ParaTrack-2 Steering Tool and the other drill string will contain the Axial Magnet Source sub or the Rotating magnet source sub. The ParaTrack Steering Tool is located inside a Non Magnetic Drill collar, behind the motor. Data is transferred up the Drill string with a series of connections allowing the passage of fluids and enabling steering information to be processed by the engineer.
The force exerted on the bit is a push force in line with the drill pipe and drillstring. The magnitude of the push force is proportional to the frictional drag force of the pipe and BHA sitting on the bottom side of the hole. To push the drillstring forward and build hole with the crushing action of the drill bit, a drilling rig must be used which is capable of the required push forces expected to be encountered. Steering control is provided by a Bent Sub, a 0.5 – 1.5 m length of drill collar with a fixed bend near the uphole connection. The bend angle and distance from bend to bit will determine the aggressiveness of the assembly. The bend angle of 1 deg – 5 deg is usually stamped at the bend position on the highside position (i.e. inside the elbow of the bend).
Jetting Assembly
Jetting assemblies rely primarily on the mechanical bend behind the jet bit to produce enough side force to change the direction of the borehole. The hydraulic power of the drilling fluid assists this mechanical action by weakening the path ahead through unconsolidated or very soft formations. In harder sections rotation or walking of the drilling head may be needed to physically assist with penetration. For directional control, nozzles may be blanked off or directed at an angle. The bit shape and configuration is usually designed to also generate directional deviation.
For example, spade bits or shovel bits are a simple wedge shaped drilling head that use the angled section to provide directional deviation. The angle of the wedged basal section will determine how aggressively the jet bit will steer, and plates are sometimes added to provide even more steering ability. These bits are ideal for drilling unconsolidated formations such as sands, peat, silt, and soil.
Bent Subs and Offset Subs are all used to provide a bend in the drilling assembly just above the drill bit. This allows the jetting assembly to be steered using push on the drill string. The normal configuration is for the bend to be located between 0.5m and 1.5m above the jet bit with the bend usually being in the range of 1 to 3 degrees. If possible the bent assembly should be made of non-magnetic material to assist with surveying.